2020 - Finished Diff. Cage
Manufacturing
Being on the Manufacturing Team meant being organized and prepared to deal with problems on the spot. If a team member presents us with a problem, we need to be able to help. Clear and constant communication across all sub-teams helps keep track of all the parts coming in and out of the shop to meet our very demanding deadlines.
2020 First prototype to visually explain design packaging of the Diff. Cage.
Printing parts helped confirm CAD design approaches. In this case, printing the Front Sprocket and a Power Adapter to test the spline design on an Off-the-Shelf differential, confirms the math used behind the splines before buying the material.
Rear Sprocket also printed for packaging visualization.
Successful part fitment confirms design approach in CAD. Note that printing does not confirm tolerancing, only part geometry itself.
2019 - Diff. Cage weighing in at 751 grams
2019 - Custom Differential machined in-house and outsourced for anodizing.
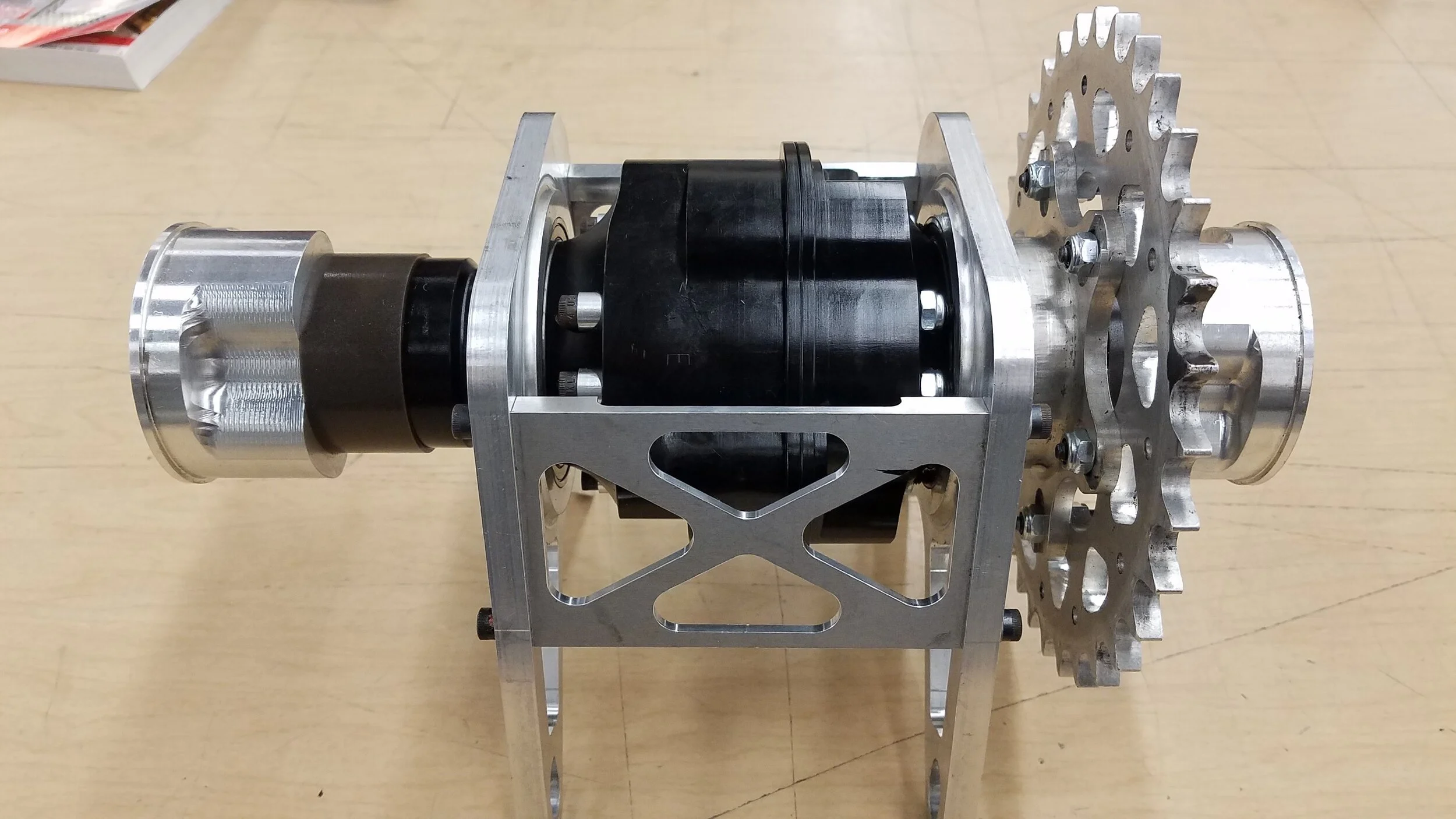
2019 - Main Drivetrain Assembly (Seen: Custom Designed Diff., Diff. Cage, Stub Axles, and Rear Sprocket)
2020 - Inventory of tools for job setups and tool replacements.
2015-2020 - Machined materials vary from Wax, Plastics, Wood, Foam, Carbon Fiber, and Metal.

2020 - Swapping out the Trunion to do 5th-Axis machining.
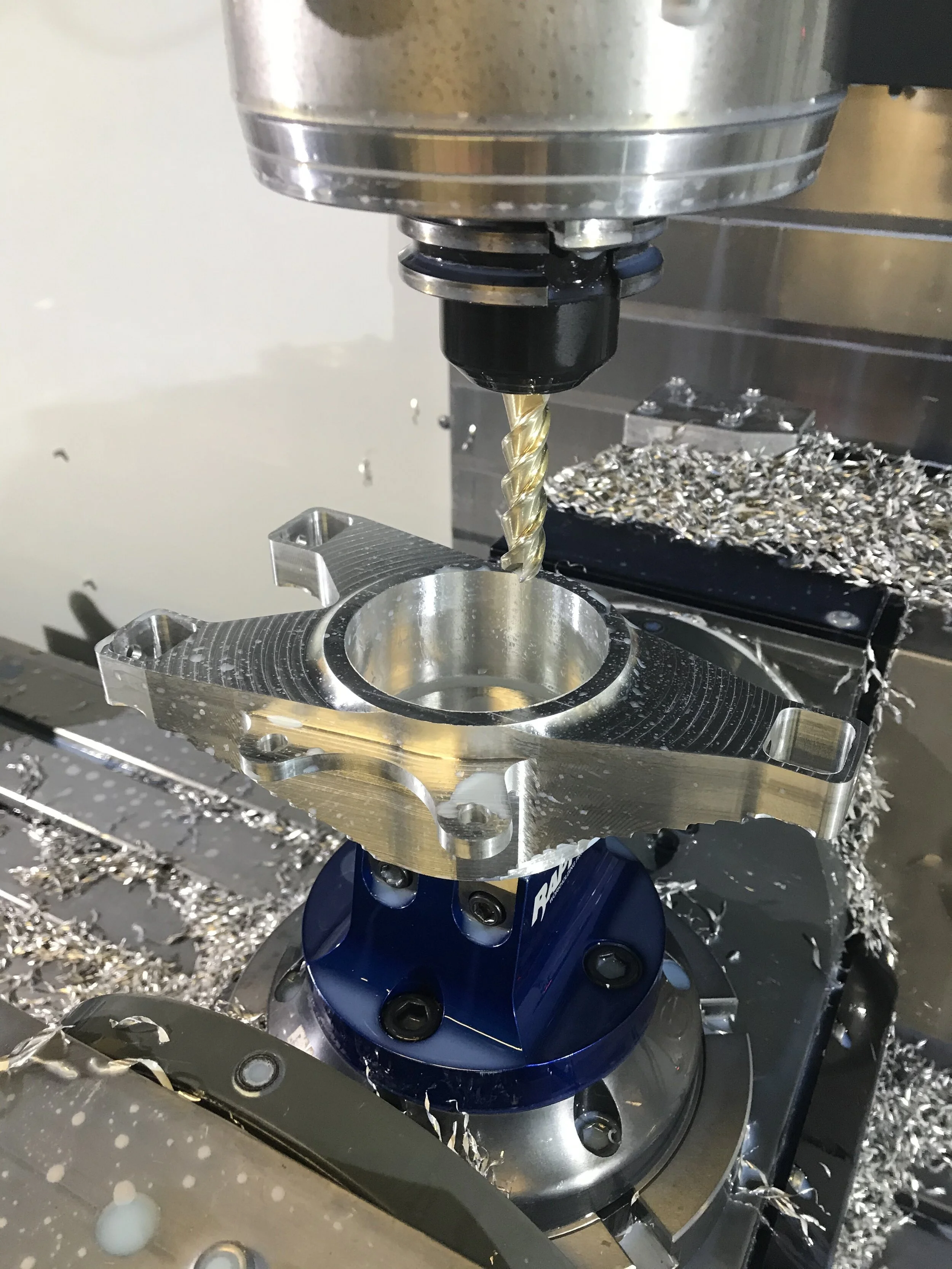
2020 - Assisting with Raptor for 5th-Axis machining.

2020 - Left and Right Diff. Plates machined from Aluminum 7075-T6.
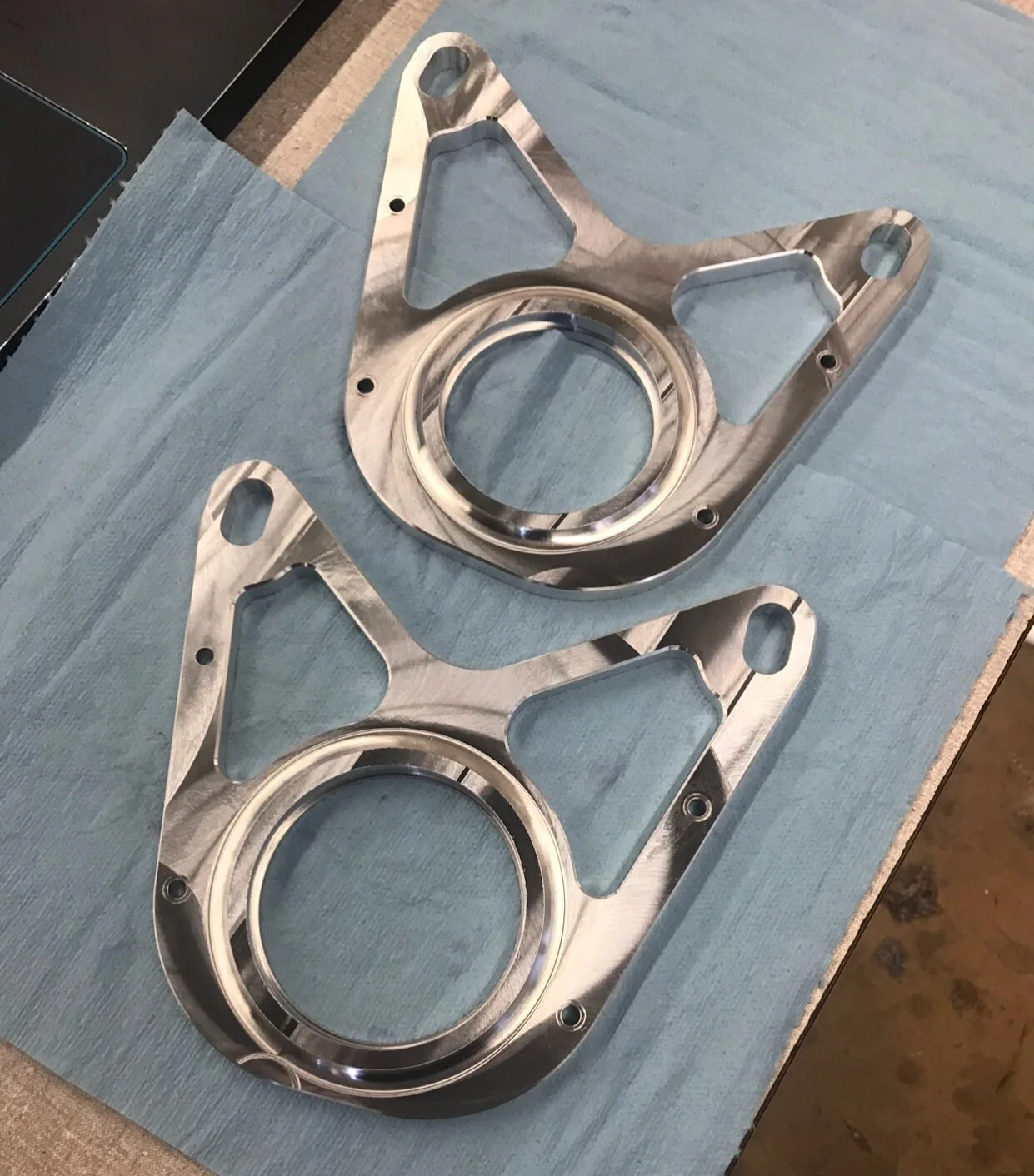
2020 - Finished Left and Right Diff. Cage Plates. Note different bearing sizes on each side.
2020 - Finished Rotor Pins turned on CNC lathe.
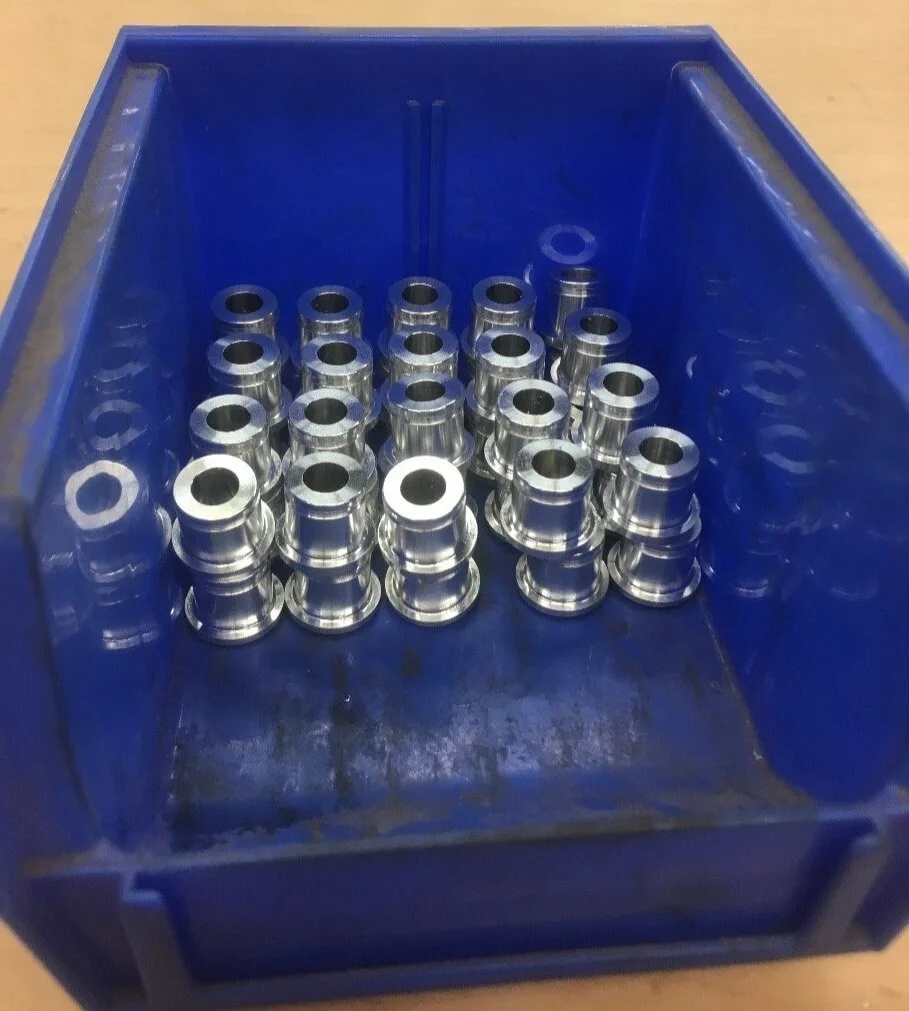
2020 - Rotor Pins for both IC and EV cars. One of several high quantity parts.

2017 - Finished Wheel Hub, Rotor Pins, and Rotors.
2017 - Wheel Hubs and Uprights.

2020 - Power Adapter for EV Car. First operation turns the major profile. Prototype of the finished product seen on the right. Multiples made to experiment with heat treatment.
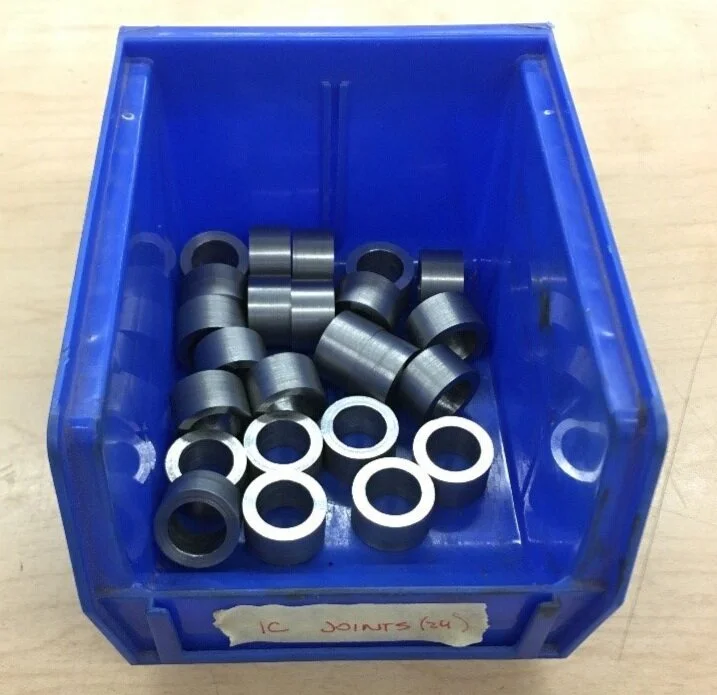
2020 - Joints to be welded onto Upper and Lower A-Arms, then re-machined after welding for Ball Joint tolerances.

2020 - Finished set of Upper and Lower A-Arms after weldment and re-machining joints.

2020 - Example of a 1 Inch Bell crank Spacer with an internal bearing Surface.
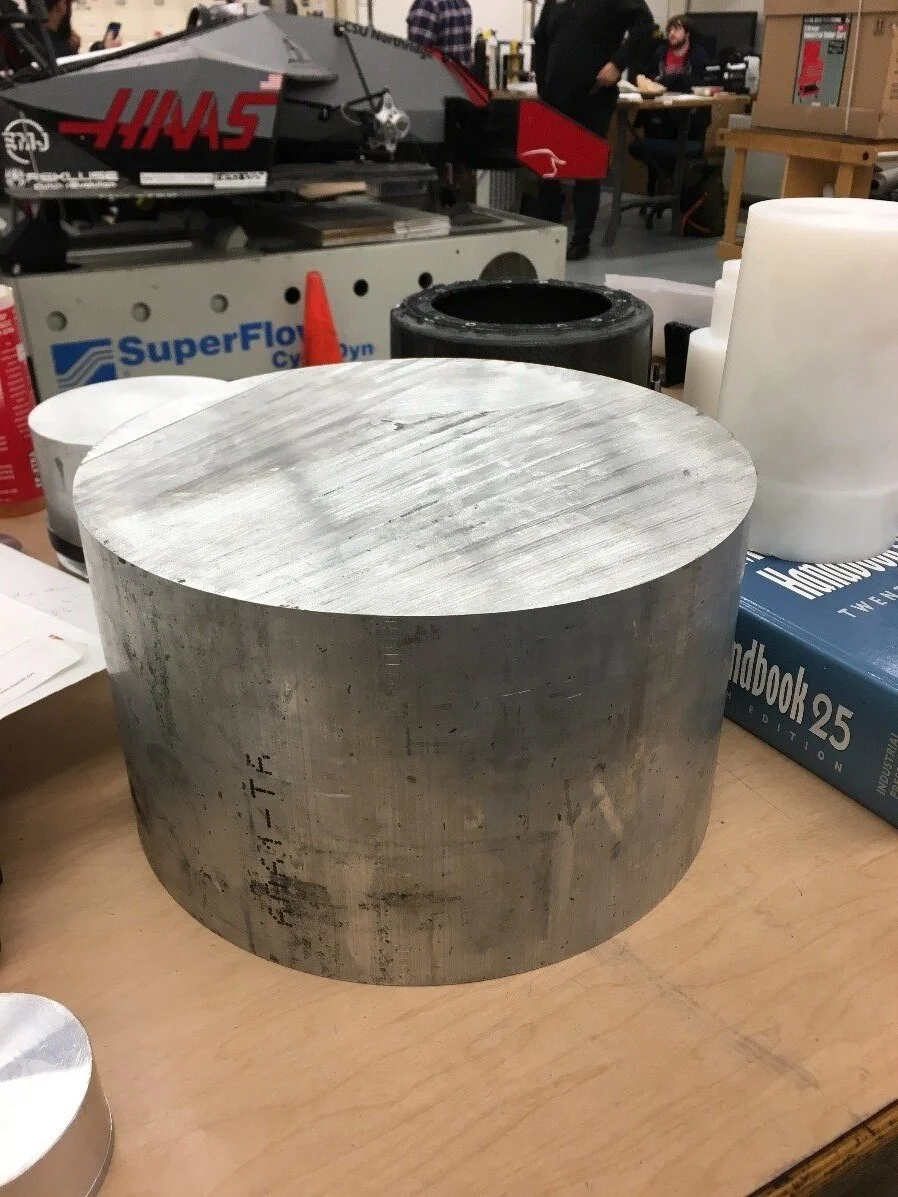
2020 - 80Lbs, 13 Inch diameter stock. Designs often pushed the limitations of the machines, requiring additional problem solving.

2015-2020 - Required to work outside the CNC Shop when machines are not available to withhold demanding deadlines.

2020 - Chassis Team Jig Table setup.
2020 - Chassis. Lending a hand when needed as well as adopting the safety and friendly policy of No One Works Alone.
2020 - Exhaust. Often assist with manufacturing methods other than machining to increase production speeds and meet testing deadlines.
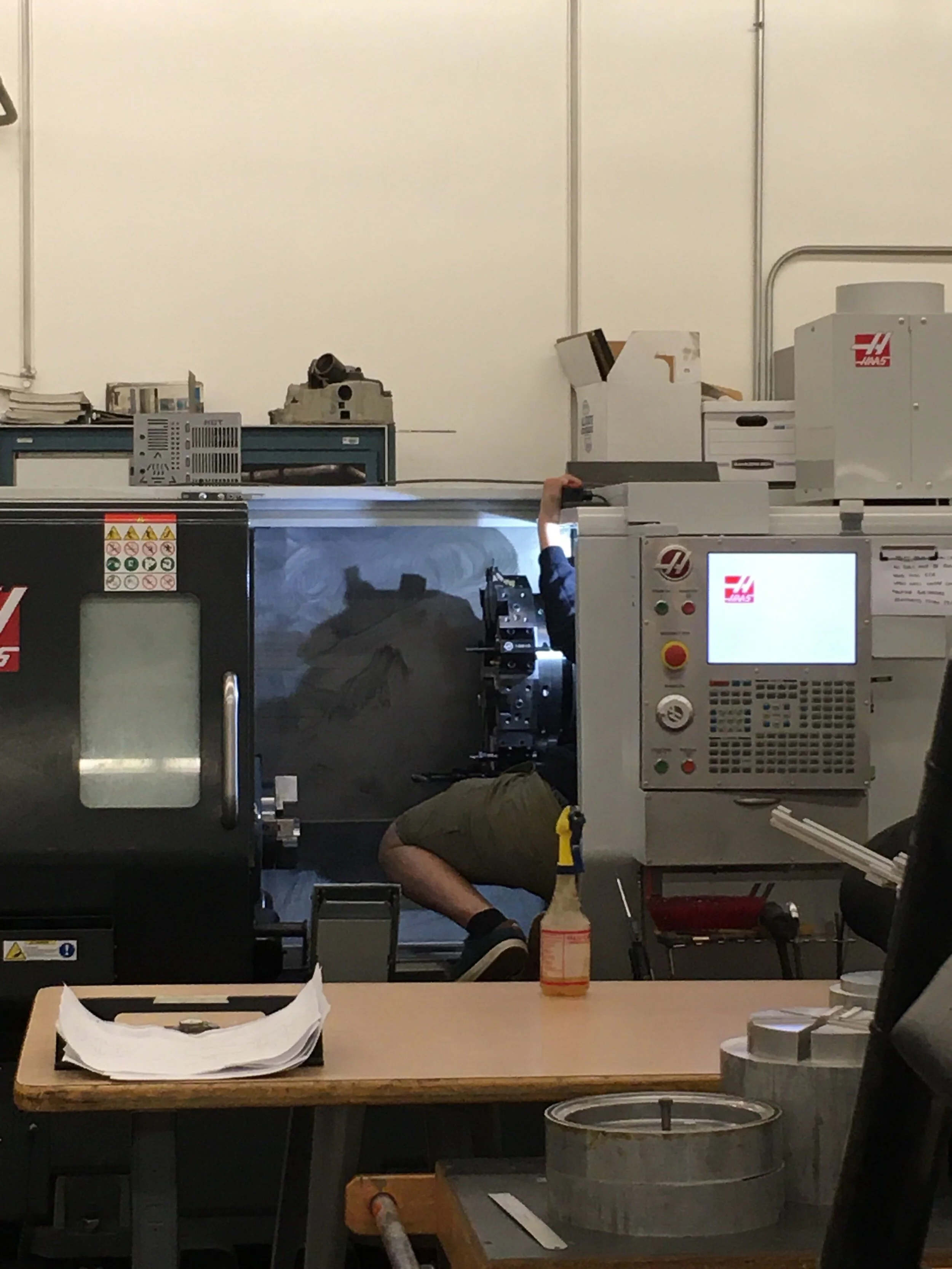
2019-2020 - Machine maintenance and cleaning to prevent rust for next year's team.